1. Melting and refining
The best iron ore is prepared in the forge that makes raw iron through the DRI process. The raw materials are processed in our in house induction forges. Once we melt our raw materials in the furnace, the molten metal is separated from the slug. Then we clean the molten iron inside a vessel furnace to attain the required composition.In this step, we add micro-alloying materials to fix the natural property of the molten metal and we remove the impurities from the mix. This is the main procedure to get properties like weldability, ductility, elongation, and strength.
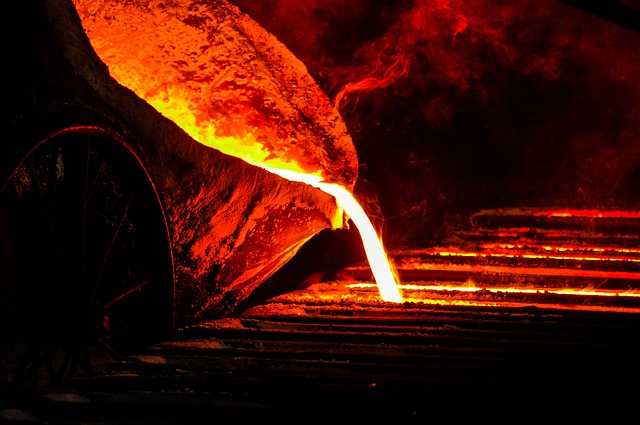
2. Continuous Casting
After the melting and refining process, the molten metal is taken into the tundish that we have taken from the ladle refining furnace. This procedure is used to make the predetermined length of metal and shaping the molten metal into the desired solidified form. This process is done continuously to the molds at a specified time to catch up with the solidifying process. With our advanced continuous casting machine, we can enhance the quality, improve the yield, productivity and decrease the cost efficiency.
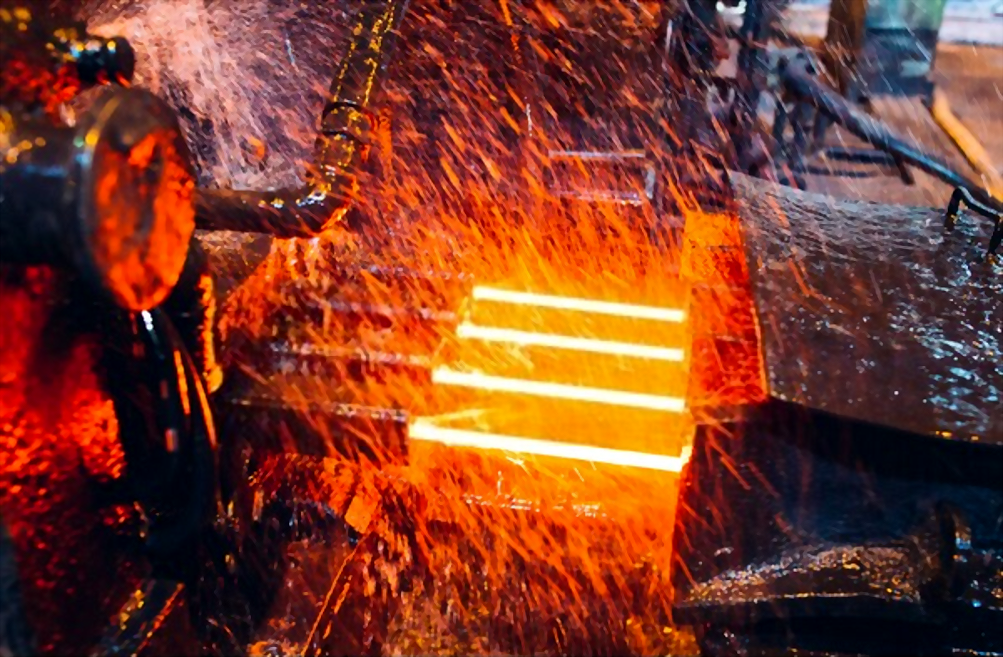
3. Cooling and Charging
Once the solid metals are passed from the continuous casting machine sent to the secondary cooling zone. Then, the semi-finished metals are cooled with water to attain the complete form. This is an important part of the cooling phase that maintains the shape of the billets, which increases the quality of the products. This step is important to recrystallize the metal to reduce the material loss and improve quality. The recrystallization process is very important because in this step the metal strands are handled in the rolling mill without damaging the bonding.
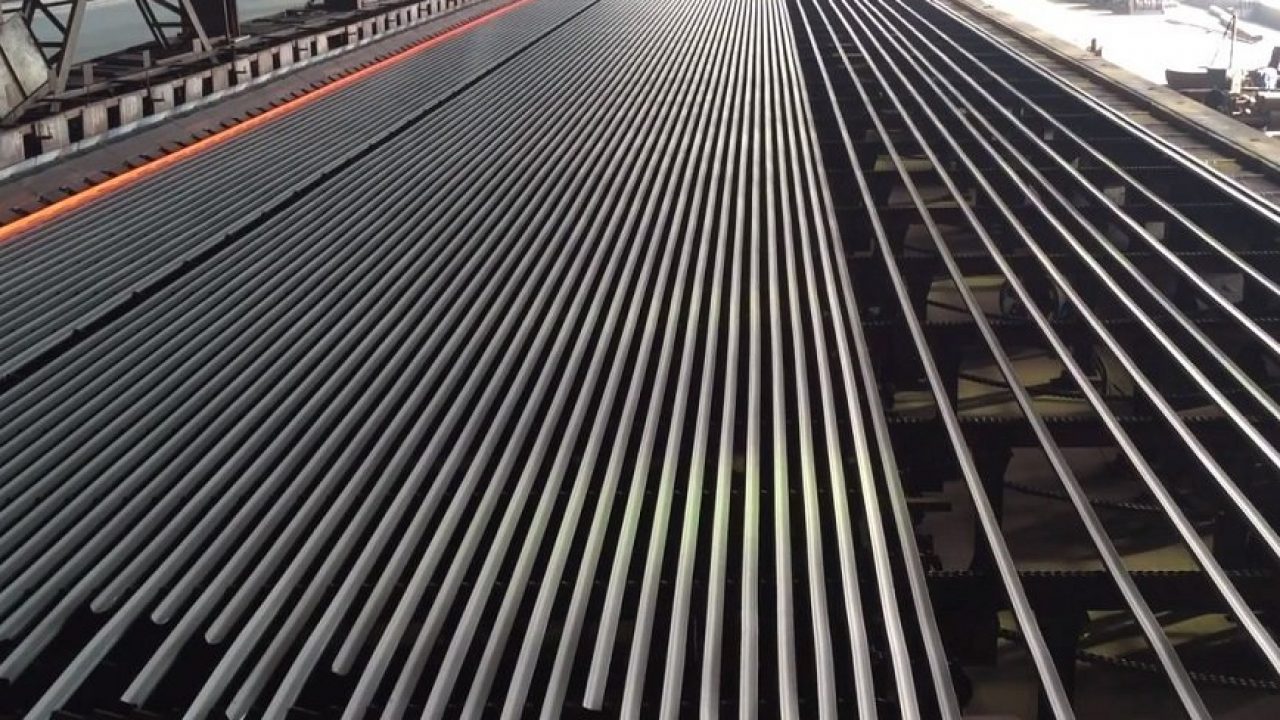
4. Rolling mill
The metal billets moved into the cutting edge rolling mill using movers. This process is done until it is passed by the international roll pass design. We use this technique to make billets with elongation and higher strength. This technique is an automatic process that is made to make the billets in uniform shape, form and ensure the same length of the bar. With our international art of rolling technology involves a roughing mill, four medium mills, and 4 pre-finishing mills and finishing mills.
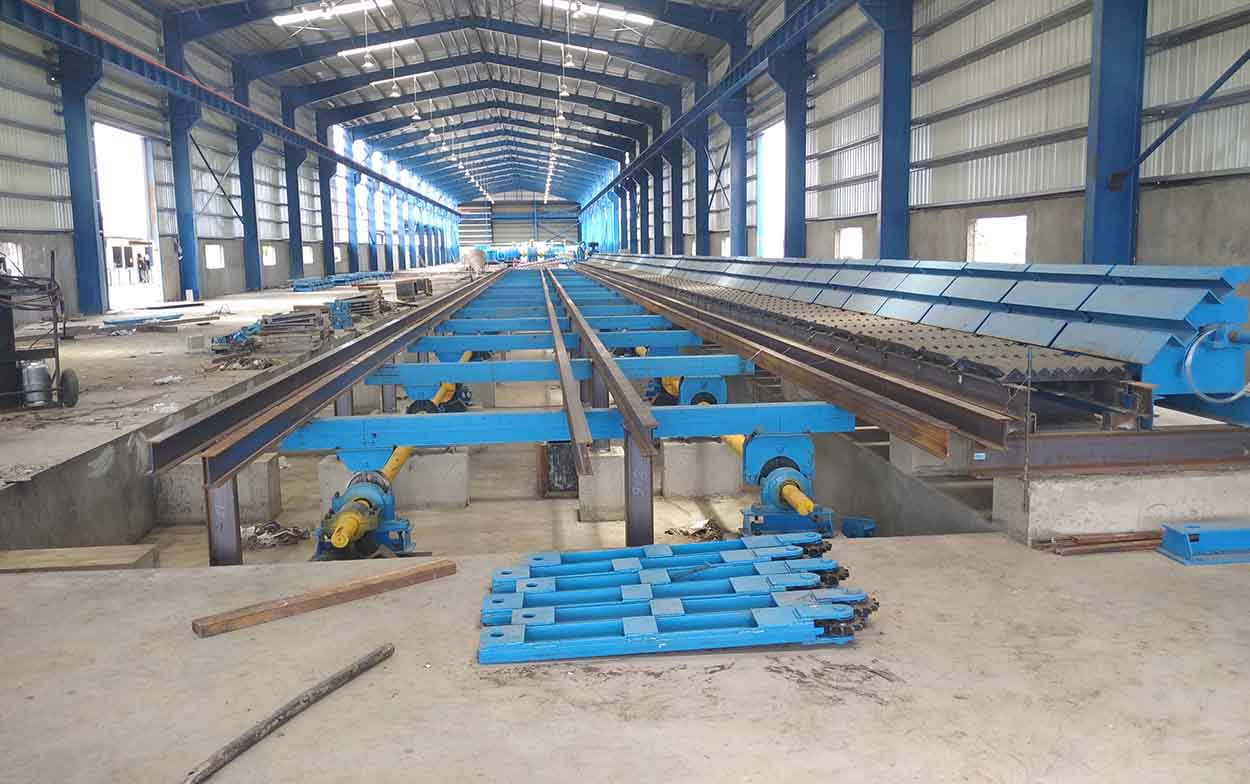
5. Quenching and Self Tempering
The steel rebars with a specified size moved into the cooling chamber and into the quenching process. With our highly advanced machines this process is completed in 3 consecutive steps.
- As soon as the steel rebars are moved from the end mill stand they are rapidly cooled to make sure the form of the bars is hardened.
- Once the quenching process is done the outer layer of the bars undergoes a tempering technique with the help of leftover heat in the furnace.
- In the last step, the steel bars are cooled in the rapid air cooling technique.
Due to this process, each steel bar will get high strength, weldability, ductility, and bendability.
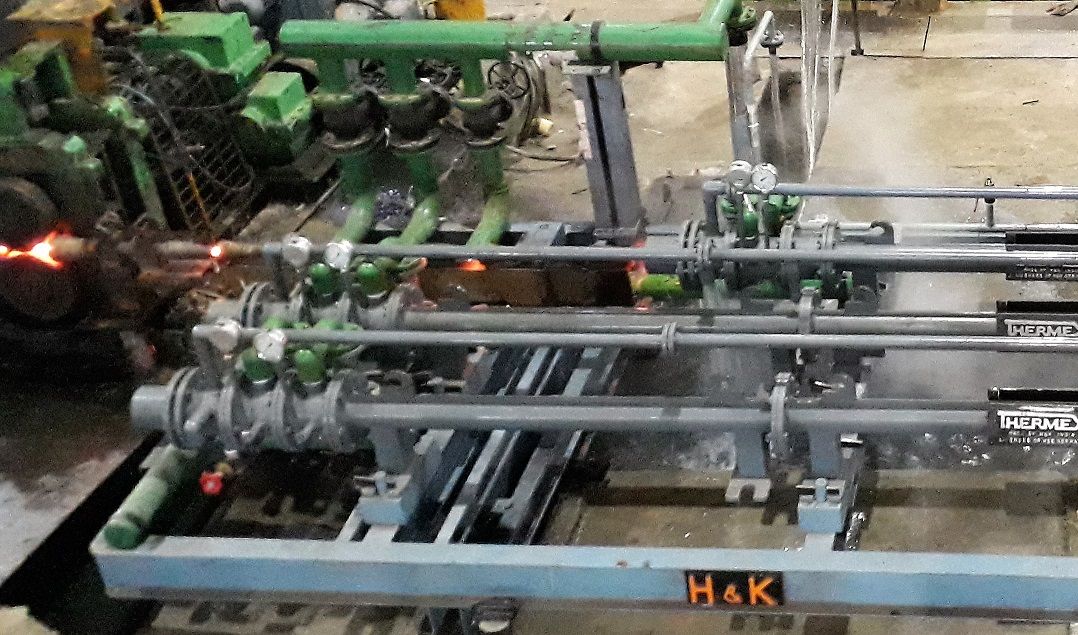